Activated carbon, sometimes known as activated charcoal, has been commercially used as a purification media since the early 19th century. Today, activated carbon comes in various forms and is used in many drinking water, industrial air and water treatment, businesses, and homes to remove contaminants.
Activated Carbon is a highly porous material that removes organic compounds from liquids and gases by a process known as “adsorption.” Adsorption is where organic molecules in a liquid or gas, are attracted and adhere to the surface of the activated carbon, as the liquid or gas passes through it.
Adsorption on porous carbons was described as early as 1550 B.C. in an ancient Egyptian papyrus and later by Hippocrates and Pliny the Elder, mainly for medicinal purposes. In fact, Archaeologists discovered that the earliest use of charcoal for water treatment dates back to around 400 B.C primarily among seafaring communities. Sailors would char the insides of water barrels to purify and preserve the water during long ocean voyages.
In the 18th century, carbons made from blood, wood and animals were used for the purification of liquids. All of these materials, which can be considered as precursors of activated carbons were only available then as a powder.
Did You Know?
Archaeologists have discovered that the earliest use of charcoal for water treatment dates back to around 400 B.C., approximately a thousand years after initial records. These findings appear across various cultures, primarily among seafaring communities. Sailors would char the insides of water barrels to purify and preserve the water during long ocean voyages.
What is the Structure of Activated Carbon?
Activated carbon is composed of a random, imperfect structure of graphite platelets and is essentially a crude form of graphite, the material used for pencil leads. This structure resembles a deck of well-used playing cards.
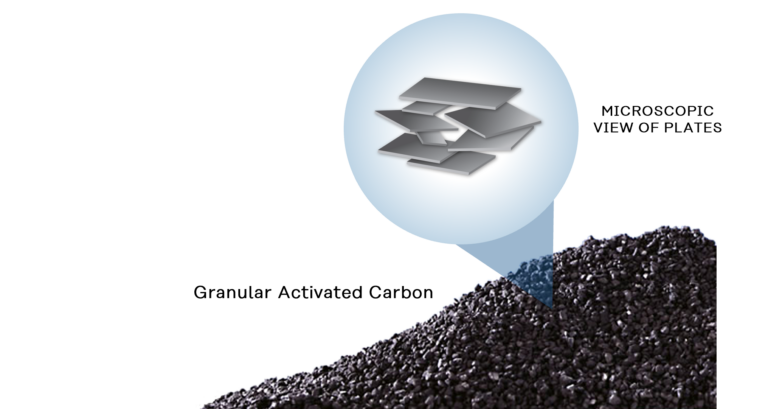
This imperfect arrangement of platelets, connected by carbon-carbon bonds, creates a highly porous structure. This structure has a broad range of pore sizes from visible cracks and crevices down to molecular scale pores. The picture above illustrates the graphitic plate structure of activated carbon at a very high magnification.
This graphitic platelet structure gives activated carbon its very high internal surface area. Activated carbon can have a surface area greater than 1000 m²/g. This means that only 5 gm of activated carbon has an internal surface area equivalent to a football field. This surface area enables activated carbon to adsorb various organic compounds from air, gases, and liquids.
What is Activated Carbon Made From?
Activated carbon can be made really from any carbon-containing starting material. However, the main requirement for a cost-effective product is that the raw material should have a high carbon content and be easy to source.
The most commonly used raw materials are bituminous coal, wood, coconut shells, lignite and peat. The raw material selection is an important parameter as it will dictate the uniqueness of the final activated carbon.
Activated carbon inherits properties from the original raw material and will dictate the uniqueness of the product and its adsorption capabilities. These are ash impurities, density, hardness or abrasion resistance and the transport pore structure which affects its performance kinetics.
The raw material selection, quality and the process to convert the carbon-containing feedstock into activated carbon, all have a significant influence on the final product properties.
For example, bituminous coal and coconut based activated carbons have different physical properties and characteristics that provide performance advantages in different applications.
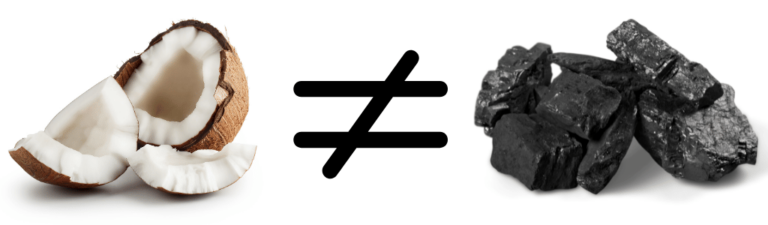
What are the Main Forms of Activated Carbon?
Not all activated carbon is the same and so the selection of the appropriate raw material, product form and properties is critical for each application. Activated carbon or activated charcoal comes in many different forms which are primarily in the form of a granular product, an extruded product or as a powder.
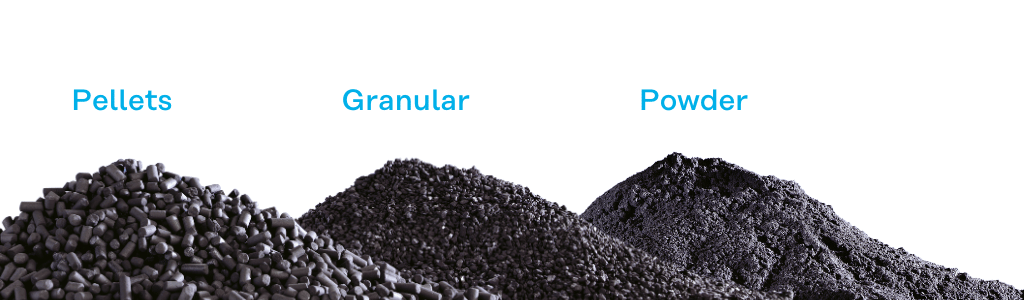
Granular Activated Carbon (GAC)
Granular activated carbon is an irregularly shaped particle crushed from its raw material form and then sized to specific mesh sizes. These sizes typically range from 0.2mm to 5 mm. The main sizes range from the coarser US mesh sizes of 4×8, 6×12, and 8×16, to the finer sizes of 8×30, 12×20, 12×40, 20×50 US mesh sizes. They can be produced from any carbon-based feedstock.
The adsorptive capacity of GAC makes it ideal for removing contaminants from water, air, liquids, and gases. Typically, granular activated carbons are placed in a filter bed in a steel or concrete vessel. In water or liquid applications, the liquid typically flows downwards through the carbon filter bed by gravity. For air, vapour or gas processes, the air or gas typically flows upwards through the carbon bed.
When granular carbon can no longer adsorb any more material, it is considered exhausted or spent. This spent granular carbon has the advantage that it can be recycled by thermal reactivation for reuse multiple times and returned to customers for reuse, instead of disposal.
Pellets or Extruded Activated Carbons
Pellets are produced by compressing or extruding the activated carbon into formed cylinders. They generally have diameters ranging from 0.8 mm to 5 mm, with typical sizes of 3 mm and 4mm. They are predominantly produced from coal but also from coconut-based feedstocks.
The production process gives them high mechanical strength, uniformity of shape, and low dust content, making them more appropriate for removing contaminants from air and gas streams.
Pellets are typically used for air and gas purification applications as low-pressure drops tend to be more crucial for these applications. Pelletised carbons operate similarly to granular activated carbons in a carbon filter bed where the air or gas passes through it. Pellets can also be recycled by thermal reactivation for reuse multiple times for the same application.
Powder Activated Carbons (PAC)
Powder activated carbons are produced by pulverising a granular activated carbon feedstock or from fines generated during activated carbon production. Powder carbons have a size predominantly less than 0.045 mm or 45 microns (<325 US Mesh) and they can be produced from any carbon-based feedstock.
The use of powder activated carbons tends to differ from that of granular or pelletised carbons. They are typically applied in batch operations by dosing or added into a water or gas stream and are filtered out later after use. In the liquid phase, this is mostly in batch operations, where the powder dosage can be adjusted to suit the particular requirement.
Activated Carbon Cloth
Activated carbon can also be produced in the form of a cloth or textile which can be in a woven or knitted form. This form of activated carbon has a microporous structure and is 100% activated carbon. Carbon cloth tends to be used in more specialised applications such as in medical or specialised clothing applications.
Impregnated Activated Carbons
Certain compounds have a low adsorption capacity on the base activated carbon. Therefore, to enhance the carbons performance, finely distributed chemical solutions can be selectively added to the carbon surface to generate impregnated activated carbons.
They are typically in pellet or granular form and are predominantly produced from coal and coconut-based feedstocks.
Impregnated carbons are primarily used in air or gas phase applications and usually for the removal of hazardous contaminants. The chemical impregnants that have been incorporated into the carbon can neutralize the adsorbed contaminants through a chemical reaction at its surface.
How is Activated Carbon Made?
There are several different ways to produce activated carbon, depending on the raw material: –
- Chemical Activation – typically applied to wood-based feedstocks
- Physical Activation
- Direct Activation method
- Agglomeration or, more correctly, the reagglomeration method
For chemical activation, the dried wood based raw material is first treated with an acid, typically phosphoric acid and then thermally activated in a kiln. The resulting product is then washed to remove any remaining acid from the carbon.
Chemviron produces both chemical and physical grades of activated carbon in Europe from renewable marine pine wood under the Acticarbone® range.
For the direct activation method, any volatile organic content of the raw material is removed during a baking or carbonising stage to produce a char or charcoal. This char is then thermally activated in a furnace and screened to generate the final activated carbon.

Reagglomerated Activated Carbons
Reagglomerated activated carbons are also produced by a multistage process. This involves the initial pulverisation of the raw material and then the addition of pitch as a binder, to produce briquettes. This is the agglomeration step.
These briquettes are then crushed and sieved to obtain granules suitable for the next steps. These granules are then baked which involves oxidation + carbonisation. They are then passed through the high temperature activation furnace, which selectively burns away part of the structure to generate these agglomerated activated carbons. Finally, the carbon is screened to produce the finished product.

Chemviron’s prime grades of granular activated carbons, such as FILTRASORB®, are produced by this reagglomeration process from selected grades of bituminous coal. This process produces an activated carbon that is uniformly and highly activated throughout the whole granule. This agglomeration process results in activated carbons with excellent adsorption properties and constant adsorption kinetics.
The re-agglomeration step generates granular carbons that are highly durable. This means that they are capable of withstanding the abrasion associated with repeated backwashing and hydraulic transfers, particularly associated with water process applications. The re-agglomerated structure also ensures a fast and effective wetting of the activated carbon when put into water or solution whilst eliminating any floating material.
This re-agglomeration process ensures that these carbons are designed for multiple reactivations where they can be recycled for reuse whilst retaining their operational properties.
If you need further advice on activated carbon or technical support to evaluate your likely treatment options, please contact us – contact our technical team.